In the pharmaceutical industry, packaging isn’t just a container—it’s a critical part of product protection, patient safety, and regulatory compliance. The materials used for pharmaceutical packaging must meet strict standards to ensure drug stability, prevent contamination, and maintain labeling integrity. So, what exactly is pharmaceutical packaging material, and how is it selected, tested, and classified?
Pharmaceutical packaging materials are substances used to produce the containers and protective systems that hold, transport, and preserve pharmaceutical products. These materials range from glass and plastics to metals and paper-based composites, each selected based on compatibility, protection level, and regulatory standards.
I. Classification of Pharmaceutical Packaging Materials
Pharmaceutical packaging materials are divided into three main categories, each playing a specific role:
1. Primary Packaging Materials
These materials come into direct contact with the drug product, making them the most critical for patient safety and product efficacy.
- Glass vials (Type I borosilicate glass)
- Plastic bottles (HDPE, PET)
- Blister packs (PVC, PVDC)
- Aluminum foil for sealing
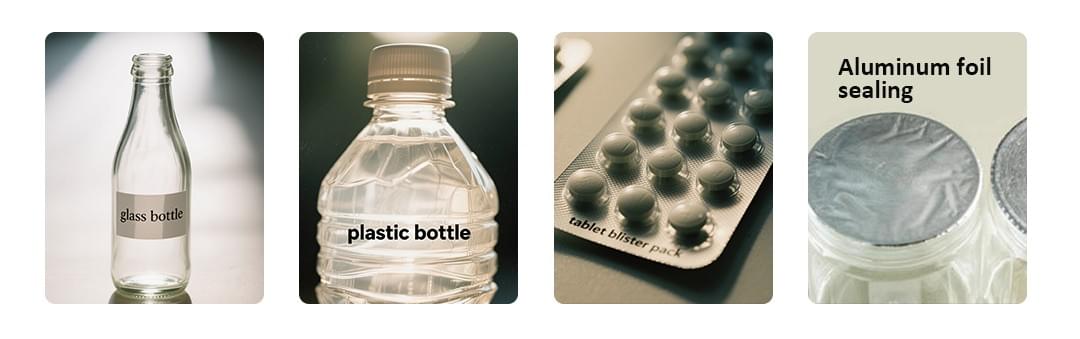
2. Secondary Packaging Materials
These materials surround the primary packaging, providing physical protection and labeling but not touching the product.
- Folding cartons
- Instruction leaflets
- Labels and tamper-evident stickers
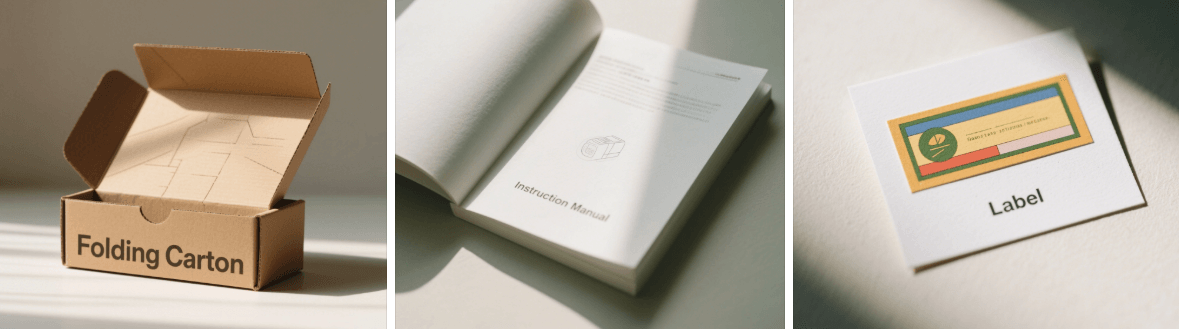
3. Tertiary Packaging Materials
Used for bulk shipping and handling, ensuring safe transport across the supply chain.
- Corrugated boxes
- Pallet wraps
- Plastic straps and crates
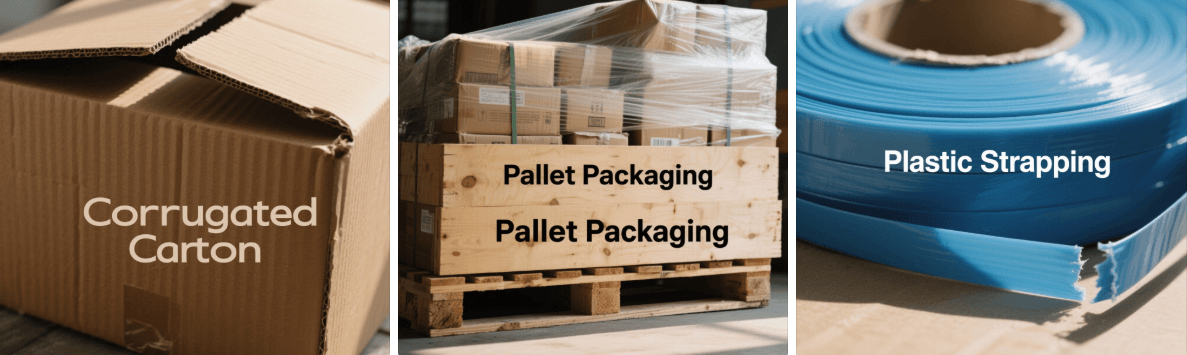
II. Common Materials Used in Pharmaceutical Packaging
1. Glass
- Types: Type I (Borosilicate), Type II, Type III
- Uses: Injectable drugs, oral solutions, vials
- Pros: Chemically inert, excellent barrier
- Cons: Fragile, relatively costly
2. Plastics
- Types: HDPE, LDPE, PET, PP, PVC
- Uses: Bottles, droppers, containers, blister cavities
- Pros: Lightweight, customizable shapes
- Cons: Permeable to gases if not properly layered
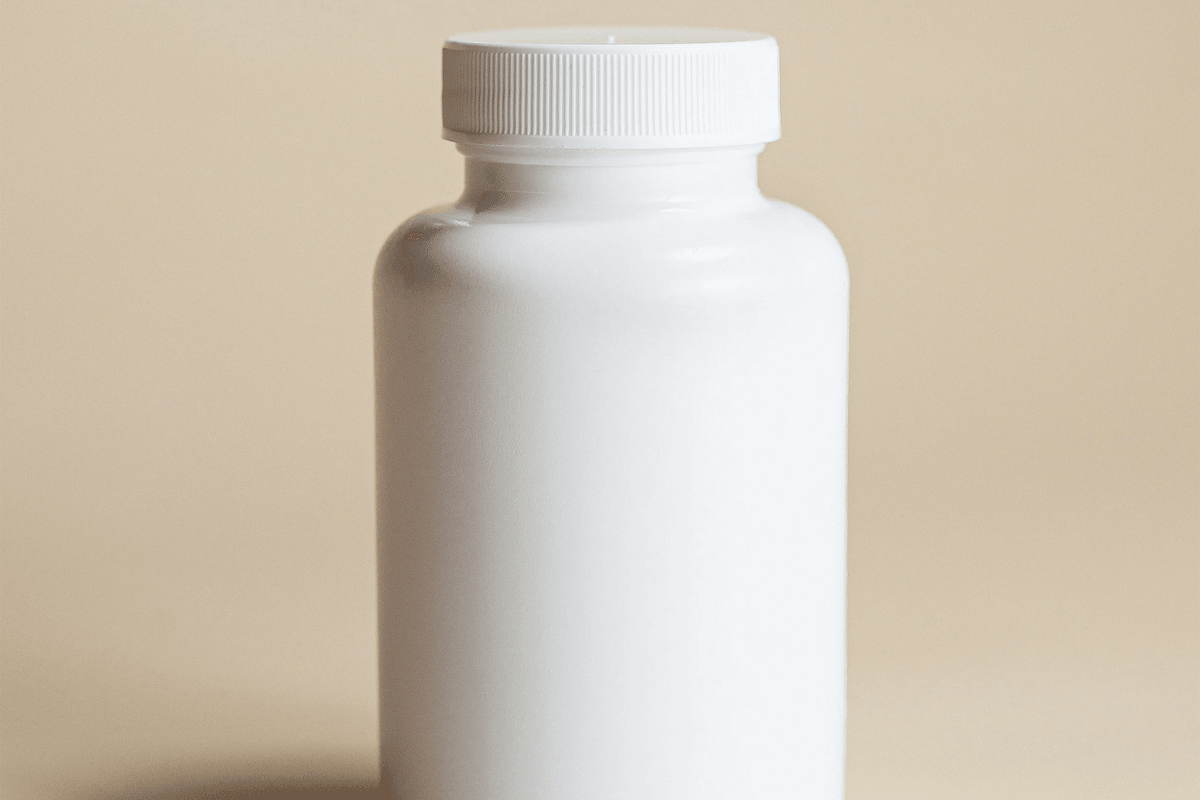
3. Aluminum Foil
- Uses: Blister backing, sachets, flexible pouches
- Pros: Moisture barrier, light protection
- Cons: Can be easily punctured if not laminated
4. Paper and Paperboard
- Uses: Cartons, labels, inserts
- Pros: Printable, eco-friendly options
- Cons: Not moisture-resistant unless coated
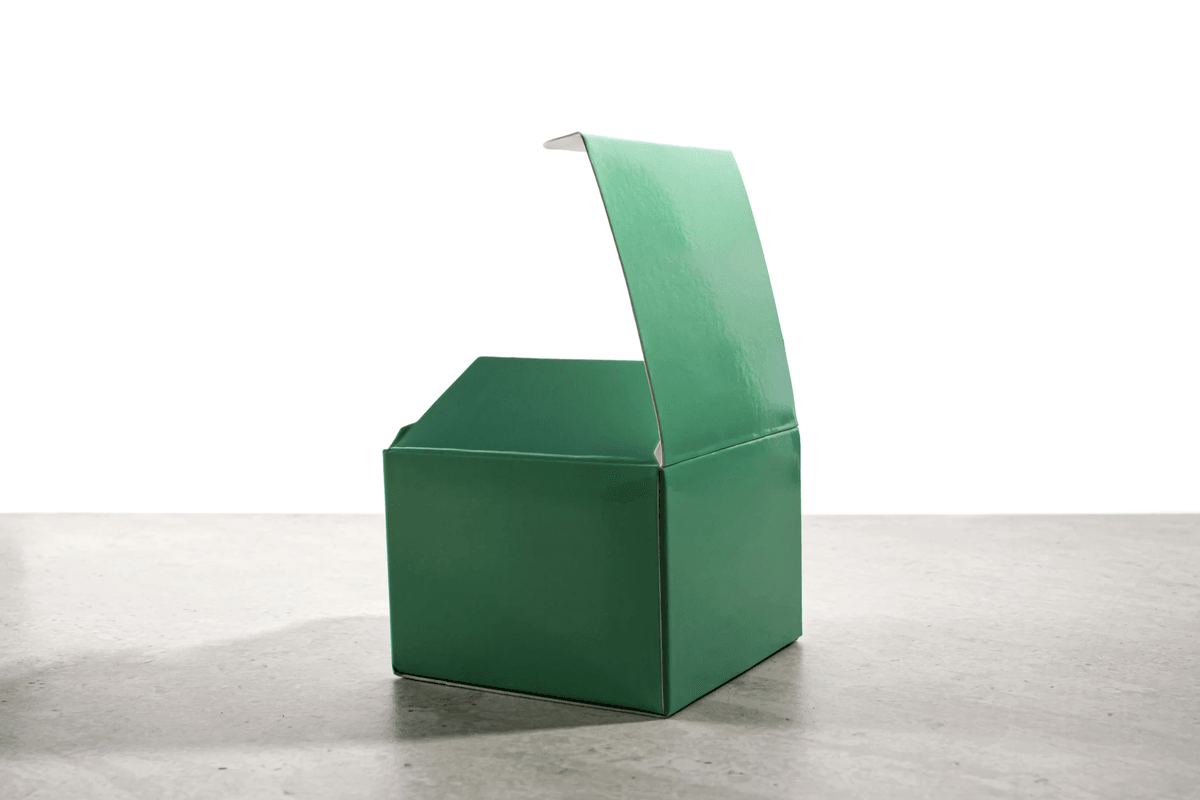
5. Ancillary Materials
- Desiccants (moisture absorption)
- Tamper-evident seals
- Cotton plugs and caps
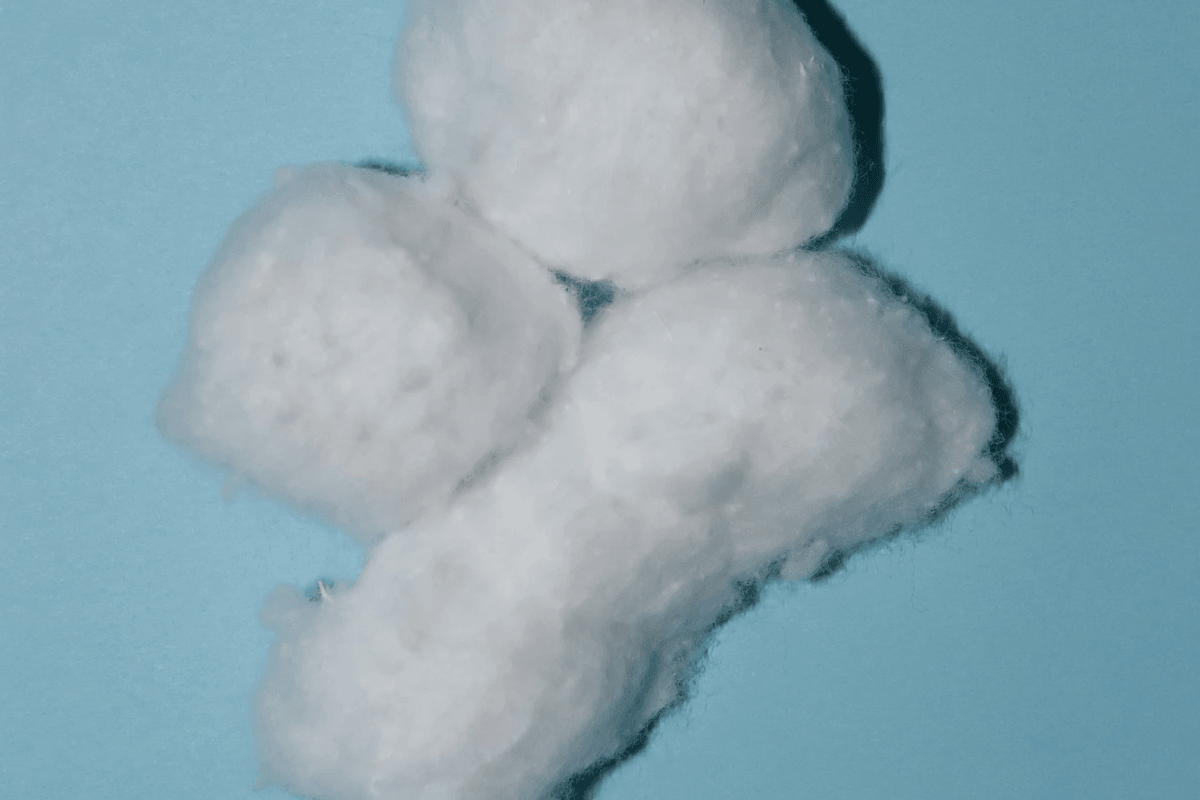
III. Selection Criteria for Pharmaceutical Packaging Materials
Choosing the right material depends on multiple factors:
- Chemical compatibility: Must not interact with the drug.
- Barrier properties: Resistance to light, moisture, oxygen.
- Sterilizability: Especially for injectables and ophthalmics.
- Mechanical strength: Withstand transport and storage.
- Cost-effectiveness: Balancing performance and budget.
- Regulatory compliance: Must meet FDA, EMA, and USP guidelines.
IV. Quality Control and Assurance of Packaging Materials
Incoming Inspection
- Visual checks
- Label verification
- Sampling based on ISO 2859-1 (AQL standards)
Material Testing Methods
- FTIR (Fourier Transform Infrared Spectroscopy): Identify polymer type
- WVTR/OTR: Barrier testing for water vapor and oxygen
- Color and opacity tests
- Leak testing for sealed packs
GMP Requirements
- Change control for material vendors
- Batch traceability and certificates of analysis
- Standard Operating Procedures (SOPs) for handling
V. Common Defects in Pharmaceutical Packaging Materials
- Glass cracks or delamination
- Aluminum foil pinholes or tears
- Deformed blister cavities due to heat-sealing errors
- Illegible barcodes or offset printing on cartons
- Cap liner failure leading to moisture ingress
These defects can directly impact drug stability and shelf life, leading to product recalls or regulatory penalties.
VI. Pharmaceutical Packaging Material Testing & Standards
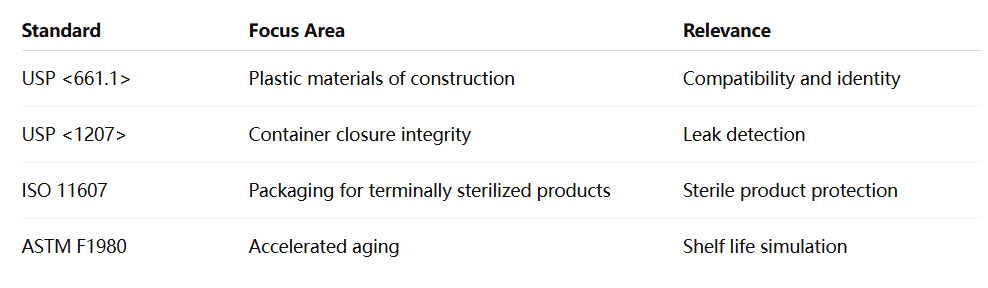
Testing must be both destructive and non-destructive, depending on the packaging type and regulatory requirement.
VII. Role of Packaging in Product Stability
Packaging materials play a direct role in protecting pharmaceuticals against:
- Moisture absorption (critical for hygroscopic drugs)
- Photodegradation (light-sensitive compounds)
- Oxidation (requiring oxygen-barrier layers)
For instance, blister packaging with aluminum backing offers better barrier properties for moisture-sensitive tablets than HDPE bottles.
VIII. Trends in Pharmaceutical Packaging Materials
- Sustainable Packaging: Bioplastics, recyclable foils, paper-based blister packs.
- Anti-Counterfeit Technologies: Holograms, serialization, blockchain-based traceability.
- Smart Packaging: Time-temperature indicators (TTIs), RFID tracking.
- Customizable Small-Batch Packaging: Ideal for clinical trials and personalized medicine.
IX. FAQs (Advanced & Practical Insights on Pharmaceutical Packaging Materials)
1. What’s the difference between packaging material and packaging in pharmaceutics?
Packaging refers to the full system including containers, closures, and labeling. Packaging material is the raw substrate (like HDPE or aluminum) used to construct these components.
2. Why is material traceability critical in pharmaceutical packaging?
It enables quick identification and isolation in case of product failure, ensuring compliance and patient safety.
3. Can different drug forms (solid, liquid, biologics) use the same packaging materials?
No. Each drug type requires unique material properties such as sterility, gas permeability, or UV protection.
4. How do packaging material choices impact serialization and anti-counterfeit efforts?
Some materials better support high-resolution coding, secure labeling, or tamper detection mechanisms than others.
5. Are eco-friendly materials suitable for pharmaceutical packaging?
Only if they pass stringent safety, barrier, and stability requirements. Most biodegradable options are still under evaluation for high-barrier applications.
X. Conclusion
Pharmaceutical packaging materials are more than just protective layers—they are part of a complex system that ensures drug safety, patient trust, and global compliance. Understanding their types, functions, and testing processes empowers pharmaceutical companies to deliver quality and compliant products consistently.
Looking for the right machinery to handle pharmaceutical packaging materials efficiently and in compliance with GMP standards?
At LTPM CHINA, we specialize in pharmaceutical packaging machines that are compatible with a wide range of packaging materials—from aluminum foil and blister packs to PET bottles and laminated films.
Whether you're packaging tablets, capsules, liquids, or powders, our machines are designed for high precision, flexibility, and regulatory compliance.
✅ Support for primary and secondary packaging
✅ Custom solutions for blister, sachet, bottle, and carton packaging
✅ Designed for GMP, FDA, and EU compliance
✅ Fast changeover and smart control systems
Get in touch today to learn how our packaging equipment can optimize your production line and reduce material waste.