Why Pharmaceutical Packaging Matters
Pharmaceutical packaging plays a pivotal role in ensuring drug safety, efficacy, and patient compliance. It protects medications from environmental factors, facilitates accurate dosing, and provides essential information to users. Moreover, packaging serves as a barrier against contamination and tampering, thereby safeguarding public health. As the pharmaceutical industry evolves, so does the complexity and importance of its packaging solutions.
Main Categories of Pharmaceutical Packaging
1. Primary Packaging
Primary packaging is in direct contact with the drug product and is crucial for maintaining its integrity. Common types include:
- Blister Packs: Ideal for unit-dose medications, offering protection against moisture and contamination.
- Bottles: Used for liquids and solids; materials vary between glass and plastic, depending on the drug's sensitivity.
- Vials and Ampoules: Typically glass containers for injectables, ensuring sterility and stability.
- Sachets: Single-dose packaging for powders or granules, providing convenience and portability.
- Syringes: Pre-filled options enhance dosing accuracy and reduce contamination risks.
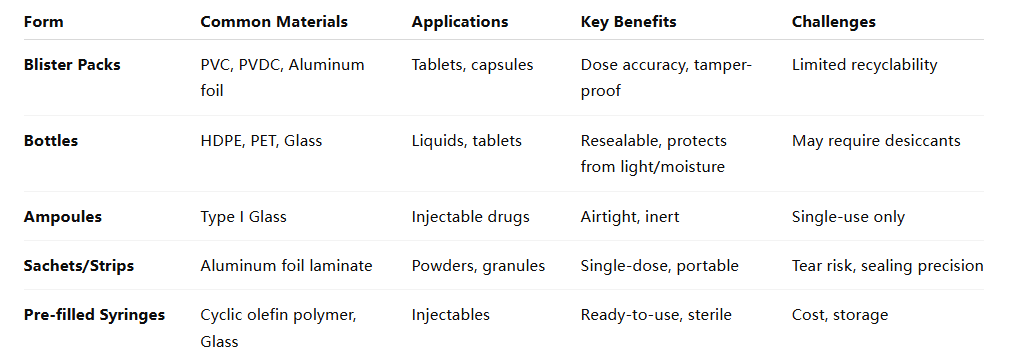
2. Secondary Packaging
Secondary packaging encloses primary packages, offering additional protection and information. Examples include:
- Cartons and Boxes: Provide structural support and space for labeling and instructions.
- Labels and Inserts: Convey critical information such as dosage, usage instructions, and warnings.
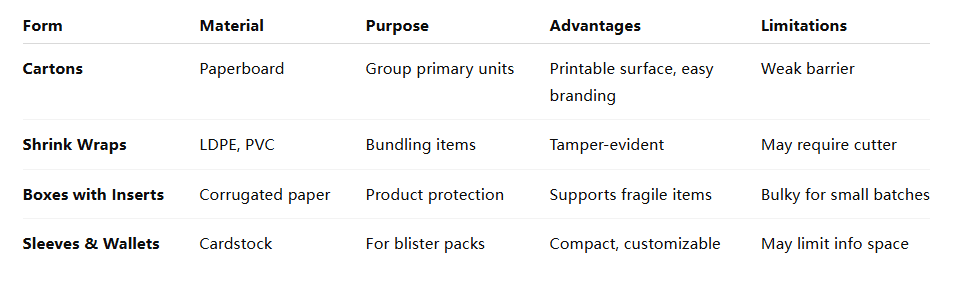
3. Tertiary Packaging
Tertiary packaging is used for bulk handling and transportation. It includes:
- Pallets and Crates: Facilitate large-scale distribution and storage.
- Shrink Wraps: Secure multiple units together, enhancing stability during transit.
Pharmaceutical Packaging Materials: Choosing the Right Barrier
Selecting appropriate materials is vital to ensure drug stability and compliance with regulatory standards. Common materials include:
- Glass: Offers excellent barrier properties and is inert, making it suitable for sensitive formulations.
- Plastics: Materials like PVC, PET, and HDPE are lightweight and versatile but may require additional barriers for moisture-sensitive drugs.
- Aluminum Foil: Provides superior protection against light, oxygen, and moisture, commonly used in blister packs.
- Paperboard: Used in secondary packaging for its printability and recyclability.
Advancements in materials science have led to the development of multi-layered structures that combine these materials to optimize protection and functionality.
Common Types of Pharmaceutical Packaging by Form
The choice of packaging often depends on the drug's form:
- Tablets/Capsules: Blister packs and bottles are prevalent, balancing protection and patient convenience.
- Liquids: Bottles with secure caps or ampoules ensure sterility and accurate dosing.
- Powders: Sachets and vials protect against moisture and allow for single-use dosing.
- Injectables: Pre-filled syringes and vials maintain sterility and facilitate ease of administration.
- Topicals: Tubes and jars prevent contamination and allow controlled dispensing.
Pharmaceutical Packaging Machines: From Filling to Blistering
Automation in packaging enhances efficiency, accuracy, and compliance. Key machinery includes:
- Blister Packaging Machines: Form, fill, and seal blister packs, ensuring product protection.
- Filling Machines: Accurately dispense liquids or powders into containers.
- Labeling Machines: Apply labels with precision, essential for regulatory compliance.
- Cartoning Machines: Assemble and fill cartons, integrating secondary packaging processes.
Secondary and Contract Packaging Trends
Outsourcing packaging operations to Contract Packaging Organizations (CPOs) offers flexibility and scalability. Benefits include:
- Cost Efficiency: Reducing capital investment in machinery and facilities.
- Expertise: Leveraging specialized knowledge in packaging technologies and regulations.
- Speed to Market: Accelerating product launches through established processes.
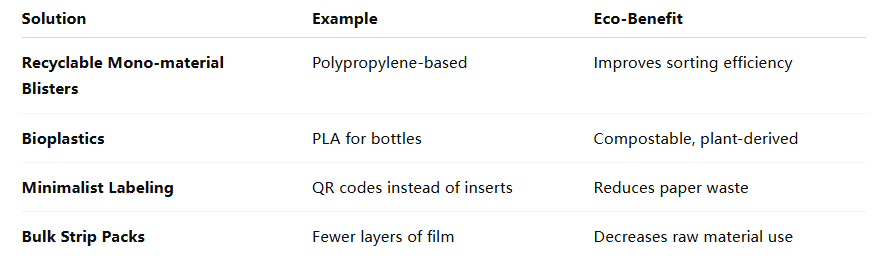
Design & Labeling: Aesthetics Meets Compliance
Effective packaging design balances visual appeal with regulatory requirements:
- Child-Resistant Features: Prevent accidental ingestion, especially in pediatric populations.
- Tamper-Evident Seals: Ensure product integrity and build consumer trust.
- Clear Labeling: Provides essential information, including dosage, warnings, and expiration dates.
Packaging Sustainability & Innovation
Environmental considerations are driving sustainable packaging solutions:
- Biodegradable Materials: Reducing ecological impact through compostable options.
- Recyclable Components: Facilitating material recovery and reuse.
- Lightweight Designs: Minimizing material usage and transportation emissions.
Regional Outlook: Packaging Standards Across Markets
Regulatory requirements vary globally:
- USA (FDA): Emphasizes tamper-evidence, child resistance, and clear labeling.
- EU (EMA): Focuses on serialization, anti-counterfeiting measures, and multilingual labeling.
- Asia-Pacific: Diverse regulations necessitate adaptable packaging strategies for market entry.
Conclusion: The Future of Pharmaceutical Packaging
Pharmaceutical packaging is evolving to meet the demands of safety, compliance, and sustainability. Advancements in materials, machinery, and design are enhancing drug protection and patient experience. As the industry continues to innovate, packaging will remain a critical component in delivering effective healthcare solutions.